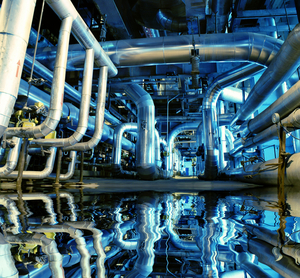
VibTech provides remote support and consultancy relating to pipework vibration assessment and problem solving. The support can also include Finite Element Analysis, which is a very powerful technique for developing options for effective vibration solutions.
Why Assessments are Vital
Many Serious Leaks from Pipework are Caused by Vibration and Fatigue
Vibration Induced Fatigue failures occur due to the progressive growth of fatigue cracks in welded connections due to fatigue mechanism. This occurs when normal operational pipework vibration is sufficient to cause large numbers of cycles of stress in the welds, such as the connections between small bore branches and main lines, which over time, cause fatigue cracks to initiate and propagate through the thickness of the pipe wall or weld metal.
Failure occurs weeks, months or often years later, when the fatigue crack grows fully through-wall, resulting in a leak, often during an extreme event such as a pipe surge or pressure spike.
Consequently, engineers often mistakenly say that the pipe has ‘suddenly’ failed due to a fatigue failure whereas in reality, the failure has been progressing undetected for a long time.
Consult with VibTech
VibTech Ltd believes that the most effective approach is for basic pipework vibration assessments to be performed by existing site staff.
Existing staff have the necessary knowledge and familiarity with the plant and with effective training, could perform >90% of all basic assessments and implement many basic remedial repairs.
However, experience shows that many companies do not have the necessary in-house expertise to be able to assess and rectify many basic pipework vibration problems and furthermore, many companies spend significant amounts of money implementing either ineffective or even more damaging solutions.
VibTech offers several consultancy services for vibration assessment.
Pipework Vibration Assessment
Guidance for compliance with industry best practise (Energy Institute Guidelines)
A pipework vibration risk assessment is a way of identifying which sections of pipework have the highest risk of failures, based on calculations, visual surveys and vibration screening. An assessment can be used to prioritise maintenance activities to significantly reduce the risk of failures by implementing relevant corrective actions.
VibTech works with many clients worldwide providing consultancy and technical support with the assessment of potential pipework vibration issues and introducing corrective actions to help to reduce the risk of vibration induced fatigue failures and increase plant safety and reliability.
This work focusses on vibration issues affecting main lines, small bore connections (SBC) and thermowells to assess whether the plant complies with industry best practice.
Whilst the majority of all vibration-induced fatigue failures will occur in small bore connections, the vibration issues originate from operational vibrations in main lines and typically originating from one of the following sources:
- Mechanical Excitation from Plant or Machinery
- Flow Induced Vibration (FIV)
- Acoustic Induced Vibration (AIV)
- Flow Induced Pulsation
- Surge/Momentum Changes
- Cavitation and Flashing
By understanding the root cause of vibration issues, then cost effective corrective actions can be implemented, such as, re-designs, bracing, supports, dampers, dynamic vibration absorbers etc.
Industry Best Practice
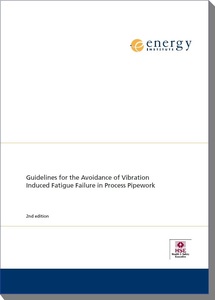
All of VibTech Ltd products, services and professional training courses for engineers are based upon the good practice guidelines of the Energy Institute guidelines, supplemented by over 30 years’ professional experience in on-site measurements, assessment and pipework problem solving.
The Industry best practice is clearly defined within a publication by The Energy Institute: ‘Guidelines for the Avoidance of Vibration Induced Fatigue Failure in Process Pipework’, 2nd edition 2008
The so called ‘Energy Institute Guidelines’ are absolutely what you should be using to ensure that your pipework complies with industry best practice. This publication defines what is good practice and what is not good practice and in the UK, is what the HSE will be looking for to ensure that your plant complies with best practice.
Although originating largely from the offshore industry, the guidelines are relevant to all industries, including oil & gas, chemical, petrochemical, food & beverage, process etc. The guidelines have been available in their current form since 2008 so there really are no excuses.
Thermowell Vibration Assessments
Assessments against ASME PTC 19.3TW 2016)
Was Your Process Plant Designed and Built Prior to 2010?
If so, your Thermowells could be at risk of mechanical failure due to fatigue cracking resulting from flow induced vortex excitation.
VibTech has developed a number of assessment techniques and is currently working with a number of companies performing such assessments, which include:
- Quantitative Assessment – desktop exercise to re-calculate the likelihood of resonant excitation.
- Onsite In-service Vibration Measurement Techniques – to detect any evidence of inline or transverse thermowell probe resonance based upon external measurements on the accessible thermowell mounting flange with the plant operational. This is often done in conjunction with Finite Element Analysis (FEA) modal predictions.
- Onsite In-service Physical inspection – to detect the presence of any significant cracks in the thermowell probe with the plant operational.
Read more about our thermowells assessment service.
Small Bore Connection (SBC) vibration Assessments
Pipework Failure Mechanism
The majority of all Pipework Vibration Failures occur at Small Bore Connections (SBCs). Frequently, small (normal or abnormal operational) vibration levels on a main line can excite increased levels of vibration of vulnerable SBCs. Poor geometry / location of the SBC can result in damaging stress levels at the welded interconnection between the SBC and the Main Line. Over time, these operational stress cycles can result in through-wall fatigue fractures and resulting leakage from the pipework (HCR).
What is a Small Bore Connection (SBC)?
SBCs refers to welded connections between smaller branch lines and main lines.
Normally the welded connection between the SBC and the main line would incorporate a standard fitting such as a ‘Weldolet’ fitting. Branches are typically 1/2” to 2” diameter and often SBCs support heavy isolation valves.
Quantitative Likelihood of Failure (LOF) Assessment Service
This is a unique data analysis service to perform all of the Likelihood of Failure (LOF) calculations contained in Sections T2, T3 and T4 of the Energy Institute publication ‘Guidelines for the Avoidance of Vibration Induced Fatigue Failure in Process Pipework’, 2nd edition 2008.
- Section T2 for 12 No. Main Line excitation mechanisms
- Section T3 for 4 No. types of Small Bore Connections (SBC)
- Section T4 for 3 No. geometries of Thermowell
These calculation methods are really useful in the following assessments
- Calculations at the design stage
- Assess excitation possibilities during trouble-shooting
- Design of Corrective Actions
How the Service Works….
Arranging for VibTech to perform your likelihood of failure (LOF) assessments is very easy, as follows:
- Refer to VibTech PV Services Price List
- Decide which types of Calculation may be applicable, e.g. Main Lines, SBCs, Thermowells etc. If you are not sure, please contact us for help and guidance.
- Contact VibTech for copies of the relevant Data Input Forms for all relevant calculations.
- Complete the Data Input Forms with all required data for each pipework location, e.g. process data such as Mass flow rates, densities and temperatures, geometric data such as diameters and wall thickness and pipe support information.
- Send the completed Data Input Forms back to VibTech together with a PO for the required services.
- VibTech will then contact you to arrange payment.
- VibTech will use the data to perform all Likelihood of Failure calculations and will produce a detailed report which will include:
- LOF results for all locations
- Intermediate calculation results for all calculations (useful for QA checks)
- Energy Institute interpretation of meaning of measured LOF values
- Recommendations for all options to reduce LOF values to below 1.0 e.g. including process changes, pipework changes, pipe support changes etc.
- The final report will be returned by email in the agreed format e.g. Microsoft Word, typically within 10 working days.