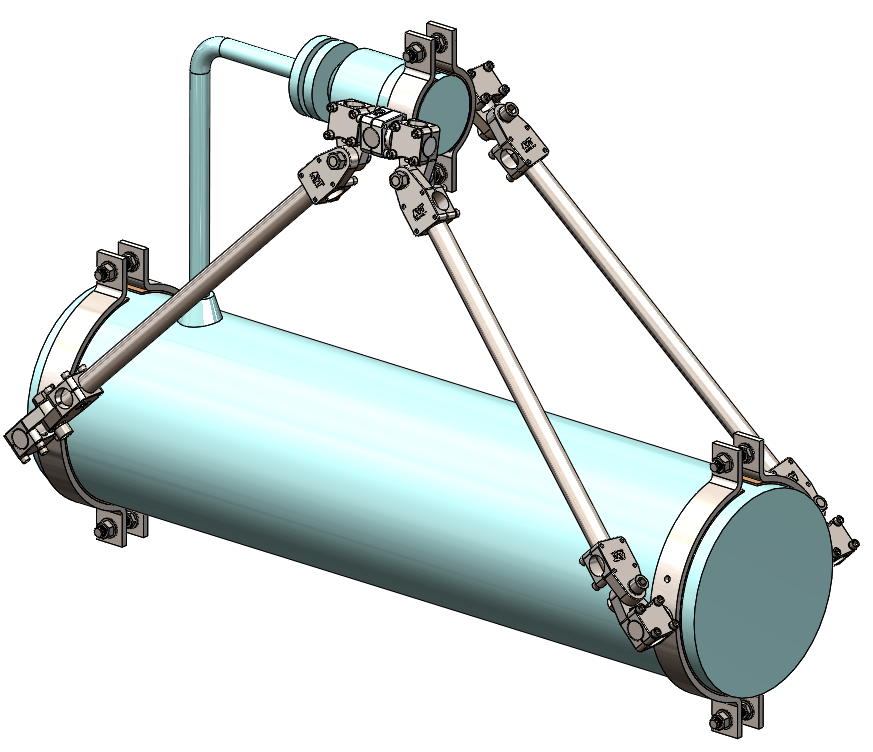
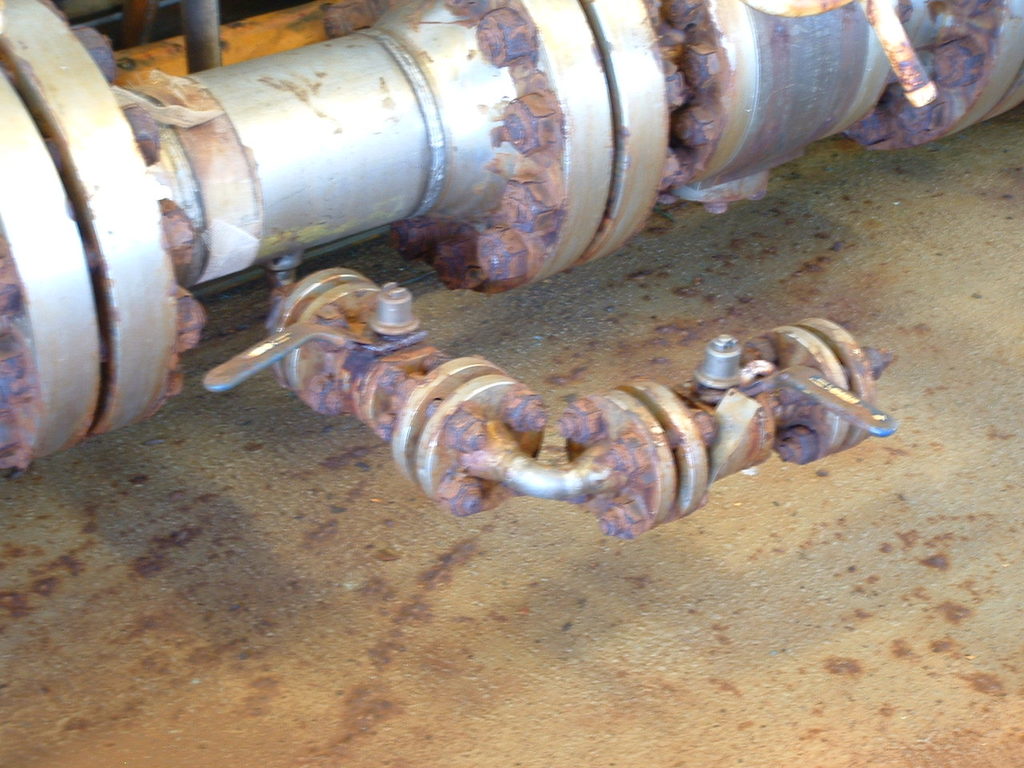
Whilst the majority of all vibration-induced fatigue failures will occur in small bore connections, the root cause of vibration issues will typically originate from operational vibrations in main lines and typically originating from one of the following excitation sources:
- Mechanical Excitation from Plant or Machinery
- Flow Induced Vibration (FIV)
- Acoustic Induced Vibration (AIV)
- Flow Induced Pulsation
- Surge/Momentum Changes
- Cavitation and Flashing
In general, it is good practice to try to address the problem at source by tackling any causes of high main line vibration first, however, in many cases, problems in SBCs can result from completely normal (unavoidable) operational vibrations in main lines and are a result of a lack of resistance to vibration of the SBC due to poor geometry or location.
By understanding the root cause of vibration issues, then cost effective corrective actions can be implemented, such as, re-designs, bracing, supports, dampers, dynamic vibration absorbers etc.
The Solutions may depend on the type of excitation and the nature of the vibration and will be different for Main Lines and for Small Bore Connections, as described below.
Small Bore Connection Vibration Solutions
The choice of vibration solutions for SBCs will depend upon whether any physical changes are possible, which would require a plant shut-down or whether a ‘retro-fit’ solution is required which could be implemented without affecting plant operation.
There are essentially 3 options
- Removal Option
- Modification Option
- Bracing Option
These options are summarised in The Energy Institute Guidelines flowchart shown here.
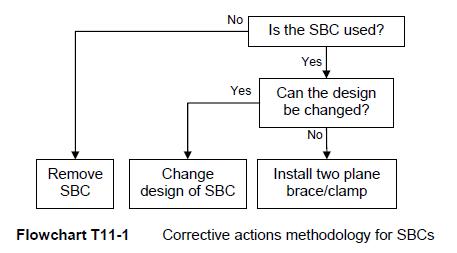
Image courtesy of The Energy Institute
Removal Option
This would be the ideal preferred solution if the SBC is no longer required.
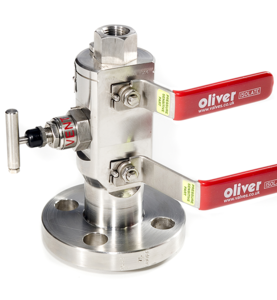
Modification Option
There are many geometric factors which affect the ‘Likelihood of Failure’ (LOF) of an SBC. In some cases, it will be possible to modify the SBC to reduce this risk factor.
Typical design changes would include:
- Minimise supported mass (Valve type)
- Minimise branch length (Type 1 & 2 SBC)
- Optimise branch length (Type 3 & 4 SBC)
- Maximise branch diameter
- Change to short contoured body fitting
- Threaded connections should be fully back-welded
Of these, the first option, to install a smaller or lighter valve type such as a Monoblock valve as illustrated is a cost effective option, which can be easily implemented without the need for welding.
SBC Bracing Option
The concept is to fit suitable 2-plane bracing to tie-back the SBC to the parent pipe such that they both move in unison and therefore any damaging stress cycles caused by differential movement are minimised such that fatigue damage will not occur.
This is normally the preferred option as it can normally be retro-fitted without affecting plant production.
SBC Bracing options include:
- Bespoke fabricated bolt-on braces
- Bespoke welded braces
- Universal bolt-on bracing solution such as ‘Easy-Brace®’
Of these, VibTech’s recommended SBC solution is the Easy-Brace option, as detailed below.
Easy-Brace
VibTech is a world-wide distributor of the Easy-Brace – Universal Small Bore Connection (SBC) Pipe Support Solution.
Easy-Brace® is a unique, patented, universal solution designed to prevent fatigue cracks at Small Bore Connections (SBC) and is guaranteed to fit all small bore connection configurations. VibTech will assist with all aspects of vibration assessment, Easy-Brace product specification, supply and installation.
Main line pipework vibration solutions
High levels of Main line vibration is normally caused by a combination of the following factors:
- Normal or abnormal operational excitation mechanisms, such as:
- Mechanical Excitation from Plant or Machinery
- Flow Induced Vibration (FIV)
- Acoustic Induced Vibration (AIV)
- Flow Induced Pulsation
- Surge/Momentum Changes
- Cavitation and Flashing
- Poor resistance to vibration (for steady state and/or transient conditions)
As a consequence, there are 2 fundamental options for main line vibration solutions:
- Remove or reduce excitation energy.
- Preferred solution as it removes energy at source.
- Often the most difficult to implement as it may affect plant production rates.
- Increase Resistance to Vibration
- Normally the simplest option to implement.
- Sometimes high energy levels can still cause high forced vibration.
Increase Resistance to Vibration
This is the most usual solution and stems from the fact that many pipework vibration issues are a direct result of poor design against vibration. Specifically, most pipework supports are designed to carry the static vertical (gravity) weight of the pipework and not to resist other dynamic forces due to vibration which can be in any direction. The resulting pipe supports designs often have low stiffness in horizontal direction, making them more prone to vibration.
Pipework often also lacks stiffness in the vertical direction. Whilst the support spacing is sufficient to carry the weight of the pipe, it is unsuitable for preventing flexing of the pipework between supports due to vibration. This is especially the case regarding the use of spring supports, which provide zero resistance to vibration in any direction.
Commonly, one of the following 3 options can be implemented to try to increase the resistance of the main line to vibration:
- Fixed Supports
- Dynamic Supports
- Cancellation techniques
Fixed Supports
This is the best and simplest option, provided the pipework does not need to accommodate thermal expansion.
However, most process pipework involves pipework at temperatures above or below ambient air temperatures, meaning that it is normal to only ‘fix’ pipework at one end and then allow it to expand on sliding supports (or spring hangers) along its length.
Sliding supports can provide resistance to vibration provided there is a good friction contact between the pipe and the sliding supports.
Visco-Elastic Dampers
Where fixed supports cannot be used due to thermal expansions (or alongside spring supports), VibTech recommends the use of Visco-Elastic Damper (commonly Visco-Damper) supports, which connect between the vibrating main line and suitable nearby steelwork.
These Visco-Damper will provide resistance to dynamic movements(vibration) whilst permitting static movements (slow thermal expansion) of up to +/- 70mm.
The also have the advantage of working simultaneously in all directions and over a wide range of frequencies.
VibTech can assist with the assessment of optimum main line solutions, including the selection of the correct size and type of Visco-Damper and the design of suitable interfacing steelwork.
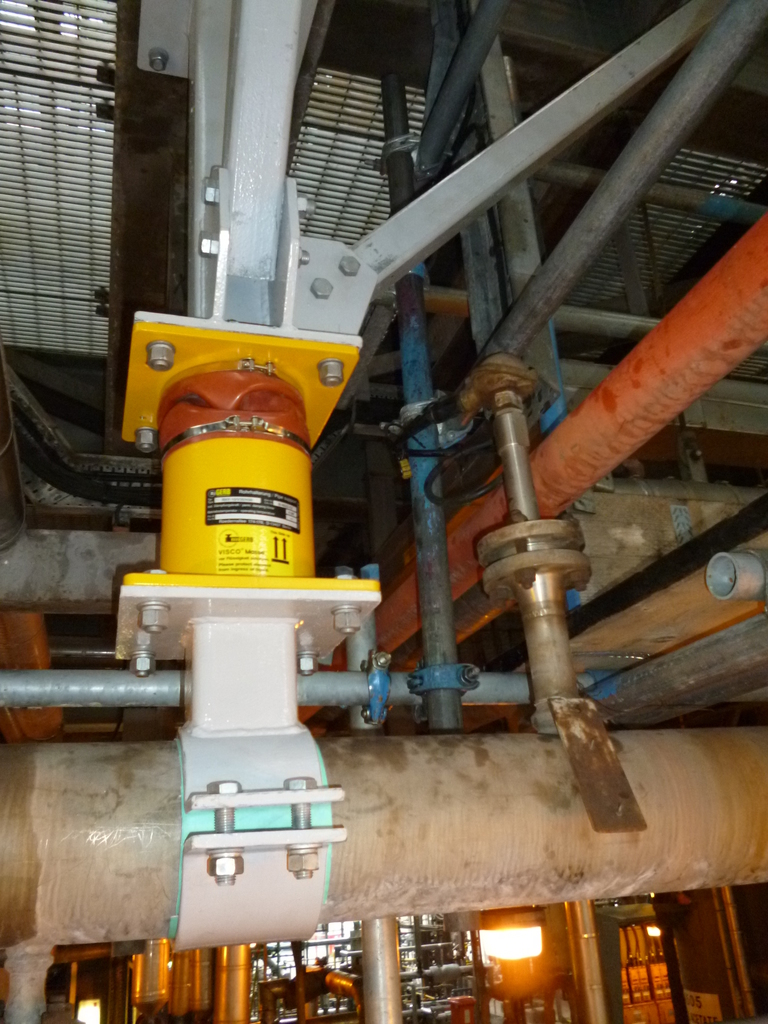
Dynamic Vibration Absorbers
Where high vibration is known to be due to resonance, where the natural frequency of a pipe is close to an excitation frequency, e.g. from a machine such as a pump or compressor, then one of the most effective solutions is a Dynamic Vibration Absorber (DVA), also commonly called Tuned Mass Dampers (TMD).
These are stand-alone clamp on solutions, designed to vibrate 180º out-of-phase with the excitation forces and thereby cancel out the vibration.
DVAs are highly effective at targeting single target vibration frequencies and producing large cancellation forces for relatively small masses.
They are particularly useful for solving tonal vibration problems such as those commonly encountered on reciprocating compressors.
VibTech can assist with the assessment of main line vibration problems and the design of suitable DVA solutions.
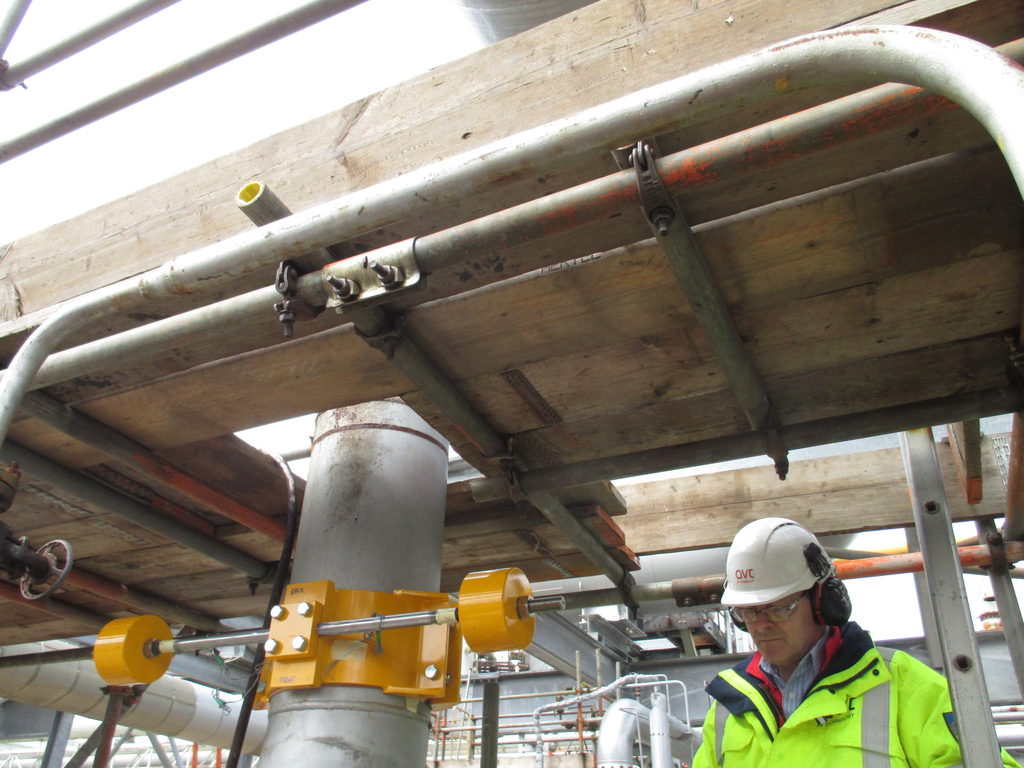
Quantitative Assessment Tool (QAT-365)
Excel based tool for performing all Likelihood of Failure (LOF) calculations
VibTech offers a unique spreadsheet based Quantitative Assessment tool (QAT-365) which will effortlessly perform all of the Likelihood of Failure (LOF) calculations in Sections T2, T3 & T4 of the Energy Institute Guidelines. It will perform up to 100 calculations at a time and is supplied as a low-cost tool with unlimited users at the same site.